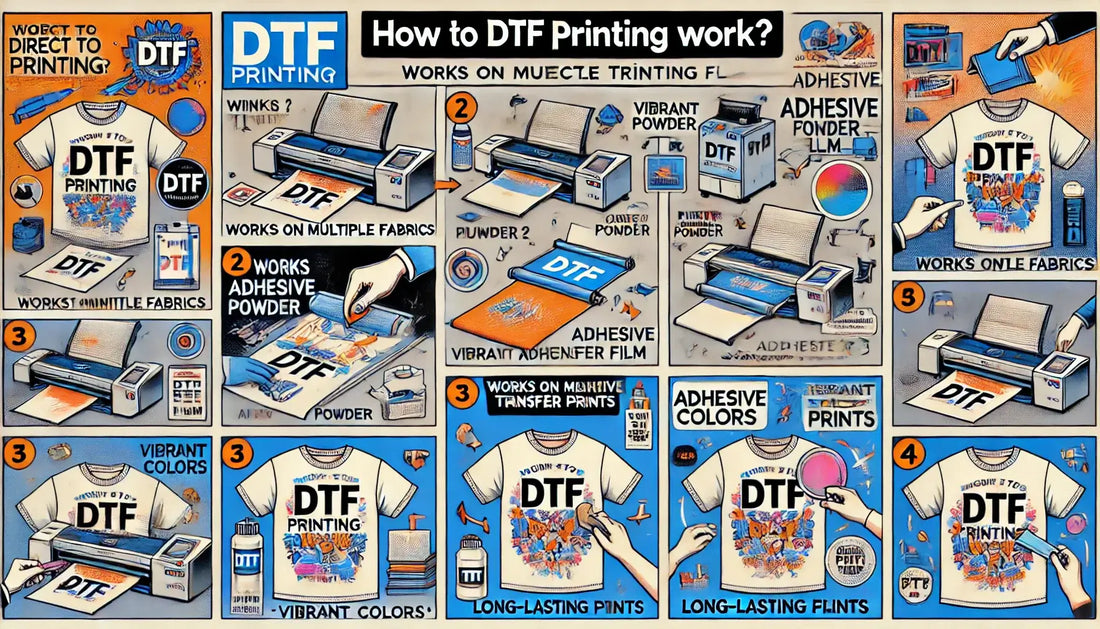
How Does DTF Printing Work
DTF (Direct-to-Film) printing works through a process of transferring digital designs onto fabric using a special film. Here’s a step-by-step breakdown of how DTF printing works:
Step-by-Step Process of DTF Printing:
-
Design Creation:
- First, a digital design is created using graphic design software like Photoshop or Illustrator. This can be any type of image or artwork, including full-color designs, gradients, and even photographs.
-
Printing onto PET Film:
- The design is printed onto a PET (Polyethylene Terephthalate) film using a DTF printer. This printer uses special DTF inks (pigment-based inks) which include cyan, magenta, yellow, black, and white (CMYK + White).
- The white ink is crucial because it forms a base layer that ensures the design is opaque and visible on any color fabric.
- The design is printed in reverse order on the film, with the color layers first and the white ink last.
-
Applying Adhesive Powder:
- After printing, a hot-melt adhesive powder is sprinkled onto the printed film while the ink is still wet. This powder sticks to the ink and will later help bond the design to the fabric.
- The excess powder is removed, and the film is then cured in an oven or under a heat press to activate the adhesive and dry the ink. This step makes the design ready for transfer.
-
Heat Pressing onto Fabric:
- The printed and powdered PET film is placed onto the fabric with the printed side down.
- A heat press is used to apply heat and pressure, typically around 300-320°F (149-160°C) for 10-20 seconds, depending on the fabric. This causes the adhesive to melt and bond the design to the fabric.
-
Peeling the Film:
- After heat pressing, the film is peeled away, leaving the design permanently adhered to the fabric. There are two types of peeling methods:
- Hot Peel: The film is peeled off immediately while still hot.
- Cold Peel: The film is allowed to cool before peeling.
- After heat pressing, the film is peeled away, leaving the design permanently adhered to the fabric. There are two types of peeling methods:
-
Final Curing (Optional):
- In some cases, the fabric is pressed again for a few more seconds to ensure the design is fully embedded in the fabric and to improve durability.
Key Features of DTF Printing:
- Fabric Versatility: DTF can be used on a variety of fabrics including cotton, polyester, blends, denim, nylon, and more.
- No Pre-Treatment: Unlike DTG (Direct-to-Garment), DTF does not require fabric pre-treatment, making it simpler to use.
- High Durability: DTF prints are known for their long-lasting quality, as they resist cracking, peeling, or fading even after multiple washes.
- Vivid Colors: The prints are vibrant and detailed, making them suitable for complex and colorful designs.
Applications of DTF Printing:
- Custom apparel like T-shirts, hoodies, and hats.
- Personalized accessories and promotional items.
- Sports uniforms and performance wear.
DTF printing is popular because of its versatility, durability, and ability to print complex designs on a wide range of fabrics.